Tungsten Solid Carbide Slitting Cutters
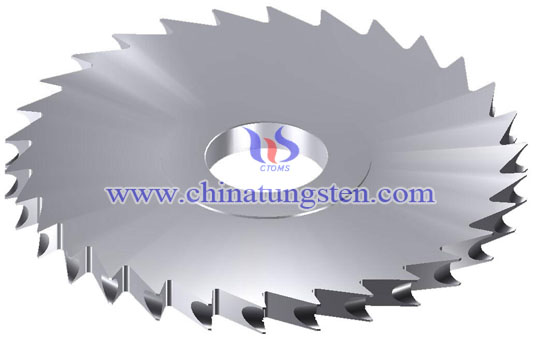
Tungsten solid carbide slitting cutters for a variety of metal materials and slit machining difficult materials, compared with the high-speed hacksaw piece cutter, high slit accuracy of the milling machining, good finish, fast productivity, long tool life, when long slit size consistency, especially for high difficult materials more superior, is textile, shipbuilding, automotive, instrumentation, petroleum, military industry, advanced tools, but also supporting similar imported machine tools.
Tungsten solid carbide slitting cutters has many advantages, but because of high-speed steel carbide itself worse than the toughness inappropriate choice when cutting process or machine accuracy is poor chipping easily, so the use of tungsten solid carbide saw blade cutter Note the following:
Tungsten solid carbide cutter blade thinner when using more sensitive to vibrations and tensile stress, if a larger radial runout or axial runout easily cause damage, so the milling machine should be run in the best condition, that is, high precision machine tools, Arbor rigid, smooth transmission, a constant amount of feed per tooth, cool sufficiently. Specific requirements are:
1. Precision milling cutter is mounted on the arbor should generally be met: radial runout ≤0.02mm, axial runout ≤0.01mm.
2. They do not affect Milling depth, as far as possible with a large flange sides of the blade is clamped on the shank. The purpose is to eliminate lateral pressure to avoid vibrations, typically the outer diameter of the flange is not less than a third of the blade.
3. Choose a reasonable milling line speed Vc and the amount of feed per tooth Sz, usually under the same conditions than tungsten solid carbide saw blade cutter selectable speed hacksaw cutter faster Vc, but each tooth feed rate should be less than the amount of feed speed steel, Sz generally set at between 0.005-0.025mm / tooth, the specific values should be based on the user's speed milling is the milling material properties, cutter diameter, factors thickness, number of teeth, milling depth of selection decisions.